ROD RATIO
An engine's "rod ratio" is the length of the connecting rod divided by the crankshaft stroke. The higher this ratio is, the better. Higher rod ratios mean less side loading on the piston and less mechanical drag from swinging the piston and rod assembly back and forth. In addition, a higher rod ratio gives more "dwell" time at top and bottom dead center.
At top dead center, more dwell time allows the pressure in the combustion chamber
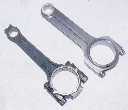
to build higher, giving more power. The tradeoff is that longer rods weigh more. Also, the length of the rod is limited by the overall block height. As the connecting rod gets longer and longer, the pin bore in the piston must be higher and higher to fit the whole assembly into a given engine. When you've moved the pin bore as high as can be, making the pistons as short as possible, a longer rod will not fit. An engineering rule of thumb is to stay above a 1.5 rod ratio, because below this point piston side loading and tensile stresses from rapid directional change at TDC and BDC become excessive.
STOCK SLANT 6 ROD RATIOS
170: 1.83
198: 1.92
225: 1.62
As previously mentioned, the bore size of all three stock Slant 6 engines is the same, 3.40". The main bearing journals and rod bearing sizes are also the same on all three stock Slant 6 engine sizes. There is one major exception: the mid-1976 and later Slant 6 engines, all 225s, have cast iron crankshafts instead of the earlier engines' forged steel crank. None of the following information will apply to them. They are not as strong as the earlier engines and have different bearing sizes. These later engines should be avoided when building a special Slant 6 engine. (Note: There are now many examples of cast crank SL6 engines being used in SL6 racing & other "high output" applications, with good success. My preference is to use the forged steel crank engines when possible but note that the cast crank engine is also a very strong unit.)
As discussed previously, boring alone won't yield a big increase in displacement. But if you combine an overbore with an increased stroke, appreciable gains in engine displacement are possible. I will present a few stroking options, all of which I have built and successfully run.