new QA1 K Frame
I never looked all that closely, but it looked like most of his stuff copied stuff designed by others.
That's what I said, and I made my point. Dillinger's stuff isn't unique, nor is it original.
Until this guys builds something that revolutionizes the hobby I think he should take a step back and shut the hell up. Its easy to look at something and say that anyone could build it.
So #1, Dillinger "revolutionized the hobbie"? Not.
#2 Name the part, I'll build it. You don't know enough about me to comment, so you might think twice before you open up on it.
Funny, I AM an engineer and from what I've seen of John's work, I'd be more than willing to install it in my car. I helped a friend install the tubular front suspension in his car and it was all quality stuff as far as I could see. I also have a set of John's tubular upper control arms and they have performed flawlessly.
He's a good guy that has worked his @$$ off to make it easier for budget-minded builds to employ better suspensions, and you're here cutting his work down because it is similar to other equipment out there.
You may want to think before you type next time. Or at least have an actual example as a basis for your claims...
-Mike
You're an engineer, huh?
So, the engineer would have said:
Heim joints have no weather seal (BAD), and no provision for lubricant (BAD). Stainless steel mitigates most corrosion but does nothing for abrasive wear (BAD). When they wear through the liner, they risk popping off (BAD), which leads to:
The heavily cantilevered bolts (BAD) are heavily loaded in single-shear (BAD), and there is no safety redundancy built in (BAD). Common sense would dictate some form of fail-safe retention like this:
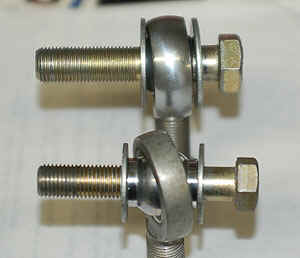
But then they might not have the travel that he's looking for (Think: which MIGHT be why a standard tie-rod is used by the OEM's instead?)
The ball-retention area is marginal for vertical loading (BAD) and I'm hoping and praying he understands the value of a taper fit, but.... Think: When one looks at the taper fit, we see that the
taper is what holds the parts together (As evidenced by the abundance of pickle forks in the world) and this taper also spreads the load through the joining parts. The taper is very thick compared to the threaded portion and that cross-sectional thickness equals shear strength. Where the ball joint (aka factory tie-rod-end) is loaded in shear is through the taper which is, as mentioned, much thicker than the threaded portion of the ball joint (The nut serves primarily to fit the two tapers together properly and provide redundant retention).
The bolts in Dillinger's kit are as small as the smallest part of the taper (If not smaller) (BAD), and are loaded in shear independent of any taper-adapters used to "make it fit" (BAD). The shear strength of those bolts is minimal compared to a proper tie-rod end (BAD), and that shear load is applied across the bolt cross section, which is much smaller than the factory taper would have been (BAD).
Not only that, but when you look around and see stuff like this:
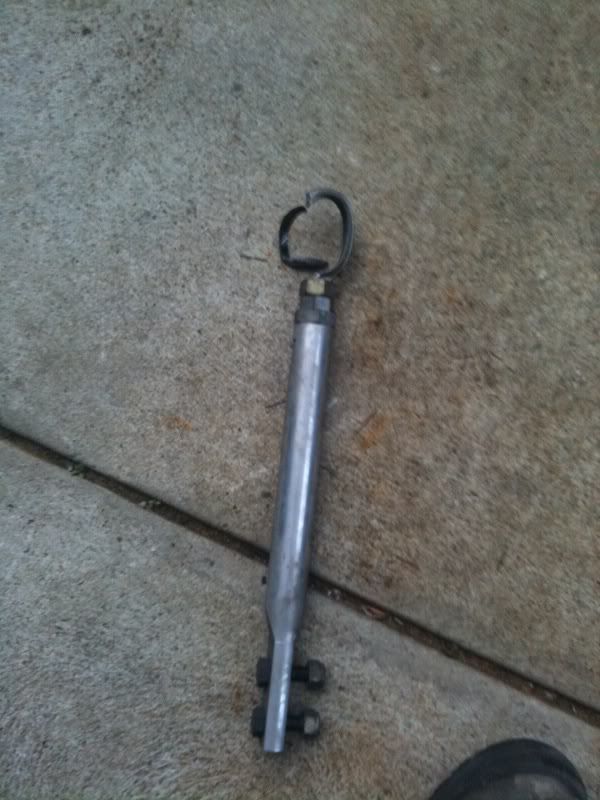
The smart man thinks twice about it. That's a heim joint, loaded in tension, pulled right apart under normal road-going conditions. Story:
http://www.aus300zx.com/forum/showthread.php?t=302985
His lower control arms have sway bar tabs loaded with a bending moment from the vertical force of the sway bar on them, but have
zero triangulation (BAD) or bracing for this vertical load or moment. Think: The sway bar controls wheel motion by limiting/applying force vertically, from the opposite wheel/suspension. How is that little flat tab handling that vertical load with no vertical support? Not well. IF he hadn't welded the bottom side it would break right off but it's still flexing (BAD), corner after corner.
Tabs:
Shown loaded in the attached photo (circled, just for you). Need I go on?
73Swingerbuild, if you're an engineer, I'd like a photocopy of your license and some background on your education. You can be an electrical engineer, a civil engineer, hell, you can be a damn traffic engineer, but it's obvious that you're a piss-poor mechanical engineer and you can still claim to be an engineer.
If there's any kind of testing data that Dillinger did before he brought his product to market, I wanna see it. Is there any tensile testing done on his welds? X-raying or heat treatment of the heat-affected zone? Is there any cyclical fatigue testing done on anything? What kind of quality control is in place here?
Was there ever before it was sold, or are you guys out driving around on it serving as his testing regimen?
But it's for sale, that means it well-engineered and safe, right? That means that you needed it and it's worth what you paid, right? I can go into more of his parts but I'm tired of typing.
Like I said, Dillinger copies his stuff from everyone else.
For the record, I don't like most of their stuff, either, and for the same reasons. You guys buy his stuff and keep patting yourselves on the back, I'm all for freedom of choice and the freedom to make bad decisions. I just hope that none of you are on a road near me.