273 rocker arm adjustment
Uuuuuh..... the notch orientation is part of the design. Proper orientation place the hole in the bottom nearly vertically downward and the 2nd hole at each rocker pointing to the adjuster side. Putting the shaft in backwards put the bottom oil hole higher and the 2nd hole in totally the wrong direction. The notch should be down and to the left on each head.
OP, your shafts for these rockers should have TWO holes at each rocker, not just one. The shafts for the standard stamped rockers have only one hole, so you may have those instead of the correct shafts. The 2nd hole at each rocker should be uphill from the bottom hole, and about 80 degree around the circumference. It is a bit larger and is important because it pushes oil through the hole in the rocker running back to the adjuster. This is the oil supply to the top cup of the pushrod and the pushrods and balls will eventually fail without this oil supply. The one cup that fell out may have overheated and then expanded the pushrod end, causing it to release. And this may be the source of your metal flakes.
The other things is that if you have a high lift cam, the pushrods may be rubbing the side of the pushrod holes in the heads. Look at the pushrods and check for any signs of rubbing on the sides.
Here is what the shafts and 2 holes at each rocker should look like; the shaft is upside down in this pix. The faint groove visible at the top is ground across the bottom hole and is for the oiling of the rocker itself. The slightly larger hole on the side nearer to the camera is the hole up on the uphill side that feed the hole in the rocker that leads to the adjuster and oils the pushrod cup. You can see the matching hole in the rocker on the rocker to the right
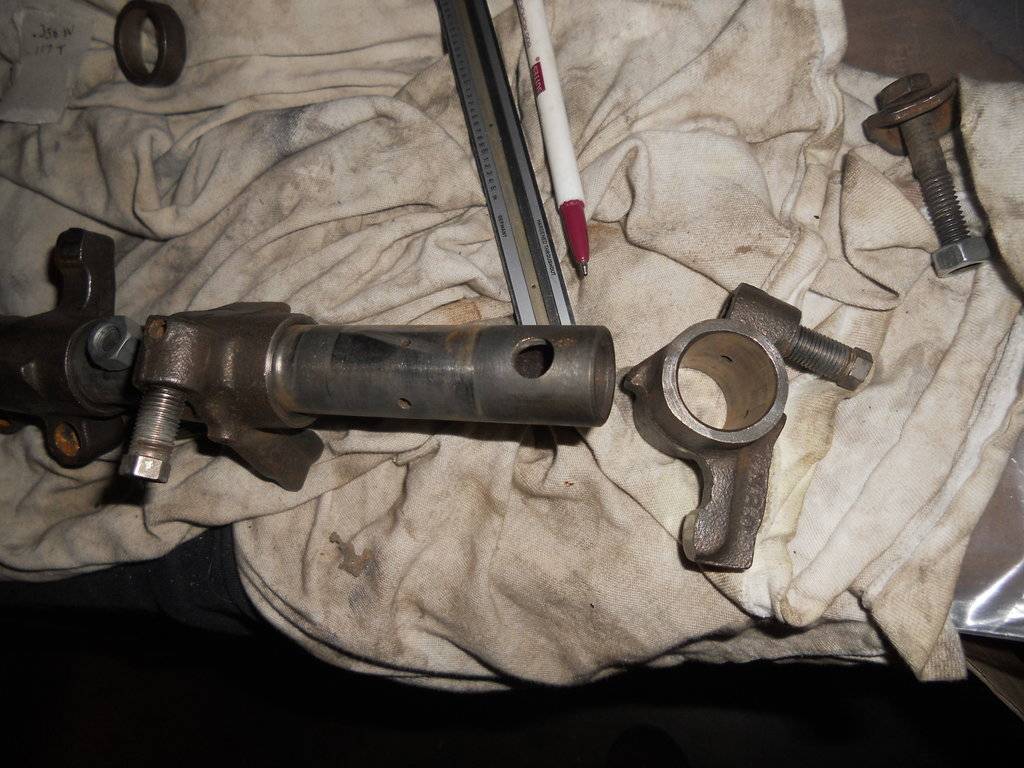