273 rocker arm adjustment
here comes another keyboard full, but wait there is pictures at the end! LOL
Do we need to be concerned that the 3 o clock and 9 o clock holes will still line up, even though they are at different angles? Green highlighted line shows it going straight through. The blue line is what we talked about doing, which would oil the push rod and valve tip side at the same time. Pink line is proposed if we dont want the two holes to line up. Now i see what your saying nm9stheham. and that is a great idea by just moving the hole in the shaft instead of the rocker arm. So lets go with the blue line for drilling the rocker arm, and then when i transfer it to the shaft, i will just measure down about 1/8" of inch. This way the two holes dont line up at the same time, so it doesnt drop the oil pressure inside the shaft.
I am going to take my springs to work to check them on the spring tension gauge tester. Do i test them at my cam card valve lift of .472" (compress them with the tool) and with the inner spring also? im not sure what they are rated for and i want to know, also i can check to see if any of them are going bad. I can see my valve locks are taking a beating, i got new ones. There is also a shim under the valve spring, and those are getting chewed on a little bit from in the inner spring.
I like the idea of making the valve tip side rocker hole a little smaller, everyone good with 3/32" .093" ?
It was a pain staking process, but i was able to get good push rod measurements for all 16 locations. I had to think out side the box in order to get it done, very time consuming. First i tried electrical tape to hold the lower part of the adjustable push rod in the hole through the head. But then it wouldnt allow side to side movement. So then i found a pen tshirt clip, modified it to fit and thats what i used to hold the lower portion while spinning/adjusting the length. Then i had to mount a rocker arm to the shaft one at time and get on the base circle of the cam to get a good measurement. I came up with a average of 7.162" from bottom of ball to top of cup. I am going to send the info off to smith and bros and OE push rods, to see who can get them done for me before next weekend.
What should i make the three holes in the rocker shaft be? I was thinking of using this nice short stiff 1/8" drill bit, and then adding banana groove to the bottom hole with a die grinder.
Another thing i was confusing myself about, is that there is no rocker arm geometry adjustment with this setup. The sweep pattern is going to be alot bigger than a roller rocker, and the roller rockers have way to adjust for geometry either at the stud adjustment, or a way to shim the shaft up or down. With this setup we cannot change the geometry, just the push rod length. seems like these rocker tips have about a .250 sweep compared to a roller rocker about about .050. So in step #3 we might not need to check the sweep pattern with dykem, just put the lazer eye on them to make sure they are centered, because the factory setup has a ton of side play, clunk clunk.
Proposed proceedure:
#1 fill the top hole of the rocker arm using brazing material. (many different methods, just avoid putting to much heat into the rocker arm). I used tig brazing with silcone bronze tig rod, DC, negative eletrode 2% thoraided, no flux.
#2 Drill a 3/32" (.093") hole under the rocker arm tip (see picture), which will shoot oil out onto the top of the valve stem/rocker tip. At this point there will be three holes in the rocker. Later on we will plug the outside hole of the valve lash adjuster threaded bore using a drill, tap, and set screw with lock tite.
#3 need to locate the rockers laterally on the rocker shafts. Center rocker on each valve tip on rocker shafts using additional shims. .015" per pair of rockers. so the order goes like this: rocker shaft clamp with bolt, then a gap, then a rocker arm, gap, stock rocker arm spacer, gap, rocker arm, gap, clamp with bolt. so those four gaps need to add up to .015", in which ever order is necessary to get the rocker arm tips centered on the valve tips. set it up with best judgement, and then put some dykem on the valve tips, rotate the engine and check the pattern. once all the patterns are good, make a diagram of how to put it back together. I only got one shim kit, hopefully its going to be enough?
#4 solder shut the existing one hole in the rocker shafts (this is tricky, im not sure how you would solder them, but i used tig braze silcone broze and a belt sander eeeekkk to grind the high spots off, also found that the shafts have a chrome or hardening coating that chips off rather easily when i tried to machine the high spots off in the lathe), polish, and then paint dykem on the shafts completely. re assemble using the diagram made in step 3 without push rods. hold the rocker tips on the top of the valve tip, this represents being on the base circle of the cam where there is no load on rocker arm from the valve springs. this will allow the oil to rush in when there is no load (larger gaps). While holding the rocker arm onto the valve tip, use a assortment of oring picks to scribe a mark in the dykem on the shafts through the rocker arm holes at 3 and 9 o clock. Drill the 9 o clock hole with a 1/8" drill bit. Now on the 3 o clock hole, measure down 1/8" and mark it, and drill that location with a 1/8" drill bit. Now somewhere between those two holes on the bottom of the shaft, drill the 3rd hole (6 o clock) in the shaft with 1/8" drill bit (this is where the rocker shaft/arm takes all the load so oil is very needed here) and add the banana groove. de bur inside and out, berry hone inside of rockers and polish everything.
#5 now we can drill tap and plug that outer hole in the rocker arm with a set screw and loctite. some of the castings are irregular, there is a couple of mine that i will have to tig weld the set screw in because there is only enough meat for a half of a hole.
#6 for the final assembly adjust everything side to side till the holes line up before you evenly tighten/torque the 5 hold down bolts. Set the valve lash to cam card specs (in my case zero lash plus one turn) cold with no lube, then take them all part and lube everything up, then double check the side to side clearance.
There is a picture of a rocker arm mounted to bolt in a drill. this is how i am going to machine the top of the rocker arm for the jam nuts. the drill represents the lathe, and the tap represents an 11/16 end mill. I will spin it in the lathe and move the end mill in with the tail stock until it just touches and smooths it up, nice and square.
I am not a big fan of harbor freight, but this little belt sander has been handy! and cheap! also the fan to keep me cool, man its been hot...
Wow this has really been a process, want to get it right, but im running outta time... i have to work 60 hours next week, and then i have the weekend and thats it...eeekkk
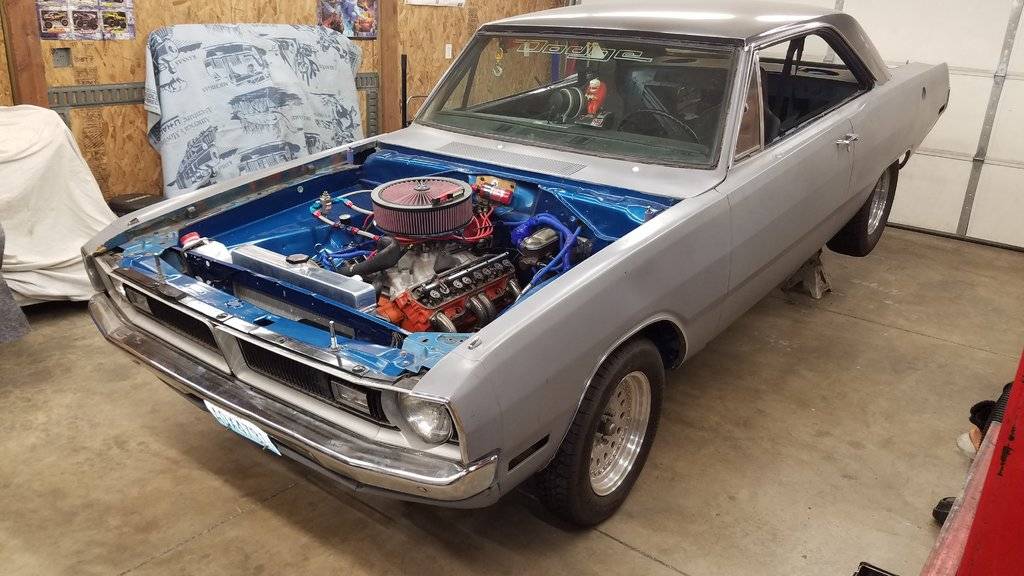