Power Valve Selection: The Definitive Answer
I agree, I believed the 2" below idle vacuum method and used a 6.5 PV. I have an A/F gauge and noticed a pretty severe lean condition at part throttle. I run about 17-18 inches of vacuum at cruise, so I will probably switch to something like a 10.5 PV so I will get some enrichment to help the part throttle stumble. Once I sort that out i may be able to lower the primary jetting.
It should be lean at part throttle. It should get leaner with more throttle. Somehow all the magazine experts somehow missed this and misled most of us for years.*
The power valve, or step up, is needed when the engine gets close to putting out maximum power for the rpm.
A somewhat practical method on a modified engine is to note the vacuum when increasing throttle doesn't bring a gain in acceleration. Then try a PV that opens at or before that vacuum.
Mike Urich, at the time a VP at Holley, discusses something like that method in
Holley Carburetors and Manifolds. Back then, it had to be done on a track with a stop watch while "crowding" a vacuum.
I've tried it using the vacuum gage and datalogger with acclerometers and its hard to do. A flat spot will show up though.
If you happened to be so lucky as to know a place with NOx gas measurement and a load dyno then it can be done by observing the combustion.
"
The purpose of the power valve selection is to enrichen the mixture prior to the combustion temperatures going too high. To set a powervalve correctly requires a NOx sensor. Different engine combinations need fuel enrichment at different power levels."
Bruce "Shrinker" Robertson.
post #4 "Another Power Valve Question" archived Innovate Motorsports forum
*
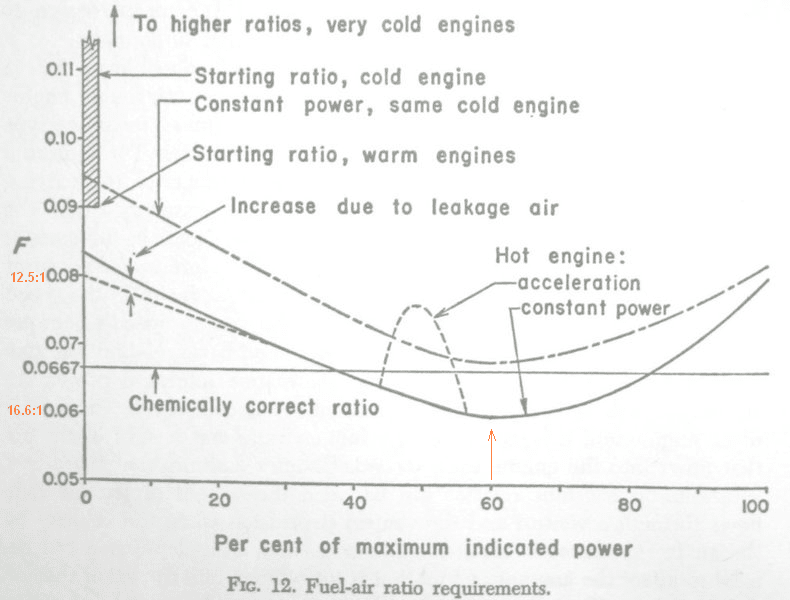
In this engine, they found it needed relatively early enrichment. That would be something like a 10.5 Power valve on an engine that cruised at 17 or 18"Hg. An engine that didn't need to go rich until 80 % load might be more like a 8.5 PV, and so forth.
Wideband