My second 1965 Dodge Dart.
One of the first things I repaired was the windshield wiper switch. I was surprised that is not made new anymore, even if you can find NOS ones around, but since my budget is not the highest, I desided to open the contraption and see what it looked like, and if I could do something with it. The switch on my car is for cars with variable windshield wipers.
As the first couple of pics shows, it is rather easy to open. The edge that is pressed in is easy to push out with a regular screwdriver if you are a little careful. Then you need a soldering iron, and it can not be too small either because you need to heat up the housing pretty good to make the solder melt.
When that is over, I held the metalhousing in one hand, and the bakelite end in the other, and separated them carefully. There are parts in the metal housing, and there are parts in the bakelite part too, and it is a pertinax plate in between. You can use my pics if you want when you open it, but if not, I suggest taking plenty of pics. The pertinax plate is not symmetric, so it will fit only one way. Pertinax is an old material that was used a lot in electronic things until they started using fiberglass. Pertinax was used for printed circuit boards in radios, tv's, and at least the 1965 Dodge Dart has it in the back of the instrument panel.
It is nothing wrong with the quality of Pertinax, and now at the age of 54, it is as good as it was when new. I have no idea if the fiberglass plates will hold as long as that.
I did clean the pertinax plate with rubbing alcohol before putting it back in place.
The switch has been lubricated with some kind of grease, at least now at the age of 54, the grease was light brownish. Can not tell how it was when new, or what kind of grease it was. Or if it actually was lubricating oil that was now hard.
Before I opened the switch, i turned the shaft to zero, or windshield wipers off. This way, when I opened the switch I could see what the neutral position sort of looked like. And I noticed that position as I lifted the pertinax plate out of the switch. Don't forget to take pictures.
In the metal housing, there are 2 major parts, well maybe we can call it 3 major parts. There are two parts with gears that has to be mounted the right way, and then there is the axle shaft. The part that sits on the axle shaft can not be mounted wrong. There is only one way to put it. The problem is the other part with the gears, how are they suppposed to be in relation to the part that sits on the axle shaft. It has gears too.
Then, when you turn the knob, because these gears makes them connected, both these parts go together. But only to a certain point. Then the part on the axle shaft with gets out of the gears on the other part, and that part will be standing still while you turn the knob and changing the speed of the wipers. Then when you turn the knob back, the gears will start interacting again, and work together. That is why it is so important that you get them together right.
I used one of these redish kind of cloth or what they are called that plumbers use to clean up copper pipes before soldering. I rubbed it over the contact points to get rid of oxydation on the copper. All the parts I cleaned well, and all the hard grease in the metal housing I loosened and wiped off, and put a piece of paper through the hole for the axle, and cleaned that too.
The contact points in the bakelite part got the same treatment, and be aware that the switch has a push in function for the washer too. It was not difficult to find out which parts belonged to that function, and I used 1200 sandpaper in between, and pushed the contacts lightly together and pushed the sandpaper back and forth to clean it up.
On my car the water tank and washer pump is missing, so I have not been able to test that function yet.
After cleaning all the contact points, I used white lithium grease on the axle shaft, and in the bottom of the metal housing and the movable parts. But not on the contact points. On the contact points I used CRC 2-26.
Since I had so many pictures it was easy to put back together, and then I pushed the edge in as it had been and got the switch closed properly.
Put it back in the car, and I already knew that would be an issue since the wires does not have one large socket, but several of them. So, I marked them how they were supposed to go before I took the switch out of the car. Glad I did, because if not, I would have been worried I did not get it right.
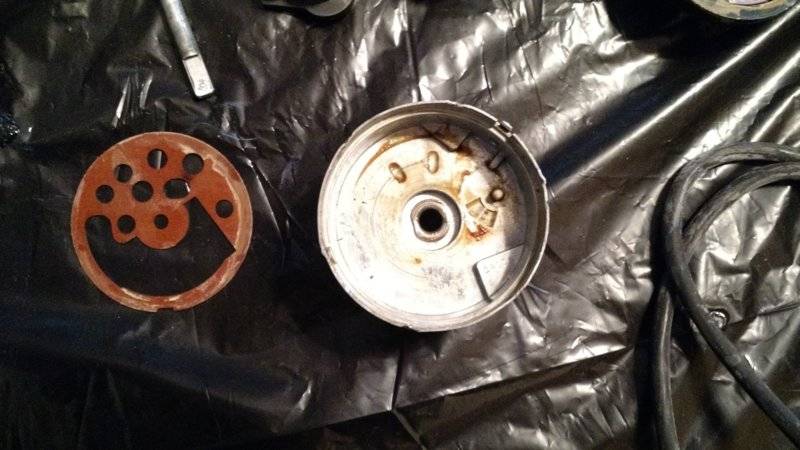