Factory ammeter
The voltage drop is proportional to the resistance AND the current flowing through that resistance.
Is this 1.5 Volt drop in the alternator output wire connection?
So putting these together, if the ammeter is showing 1/2 way up the charge level, that's about 20 amps to the battery.
The alternator field and the ignition are taking abother 5 amps. So that's about 25 amps through the alternator output wire.
Its not clear to me whether the newer one is acting up, or is cabable of providing much power at idle speeds than the old one.
All alternators produce much more power above idle speed. Lets say when regulated to 14 v the old one maxes out at 25 amps at 650 rpm, and the new one can produce as much has 45 amps at 650 rpm. And lets say the battery is low and when given power at 14 V will try to draw 50 amps. That creates lots of problems most of which are obvious - such as 40 amps is more than the circuits are made to handle - charging a battery that fast will cause it to get hot and charge poorly - maxing out the alternator is hard on its wiring. Another is that the voltage drop at the connector will be nearly twice what it was with 25 amps flowing through it. Voltage drop = current x resistance.
I would start by cleaning the terminals. Tighten them up as needed and make sure they are secure when you reinstall. Look at the wire condition at the crimps as well.
You can find some posts about disconnecting the bulkhead connector, as well as removing the male and female terminals.
New seals are available from DMT.
If the terminals are compromised there are a few different ways to improve the flow path.
Some people drill straight through the connectors and join the wires. I don't like that because it makes it difficult to service and diagnose any of the other circuits in that connector.
My suggestion is to take a cue from one of the methods mopar used when installing high output alternators. The most common one people have posted photos of here seems to be on cars equiped with rear window defroster grids.
What I did on my '67 was a parallel wire feed to terminal stud. This is similar to what Chrysler did for some 60 and 65 amp alternator equiped cars with options other than the rear window defrost.
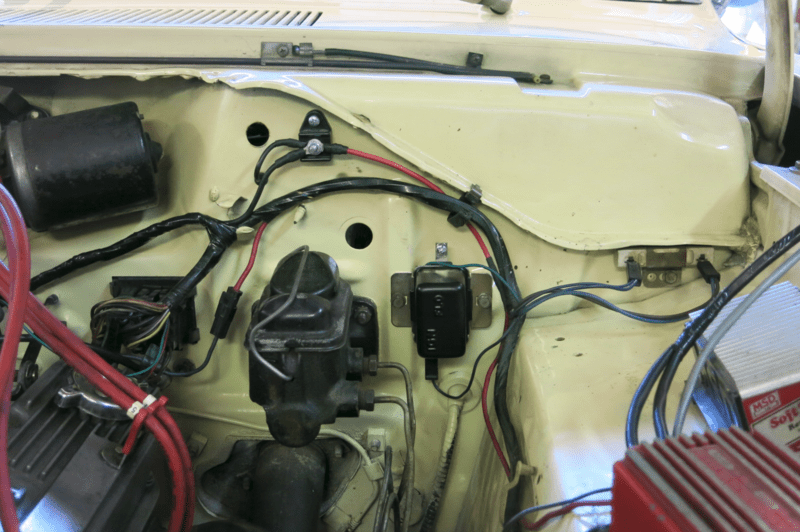
I chose to use the terminal mounted in the factory location because I wanted to power the MSD, and didn't want it pulling power through the ammeter.
In this car the alternator output terminal in the bulkhead was OK, but had some overheating damage. Damage I can almost certainly pin on a low battery recharging situation.
So the way its wired now there are two paths from the alternator to the main splice. Current will take the path of least resistance, normally the shortest but this way there is some redundency.
If you have no need for a terminal stud, you can run the parallel wire direct through a grommet to the ammeter's stud. This assumes your ammeter is relatively accessible and that it is an internally shunted ammeter.
Anyway the point is there's a number of ways to skin the cat besides drilling through the existing connector.