Reinforcements for whole floor removal
Heres pix of inner fender and main floorpan I removed for replacement due to rust and butchery. I cut it out with a cutoff wheel, leaving strips of the old metal spotwelded, then using the rotary file, grind the spotwelds down on the side I was discarding, then using the hammer and sharpened scraper, slip the scraper between the metal sheets your separating, and hammer into it to seperate, and peel it out. I would recommend the same on your floor replacement. You can see my 8 year old son separating spotwelded pieces on a parts car i ground down with the ball rotary file. This method makes it really easy to seperate it. Just wear gloves or you get steel splinters in your hands.
Remove the old floor in large chunks being very careful to not cut into any brackets or anything you need to save. If using a cutoff wheel to remove sections of old floor, cover up everything including the glass. Red hot sparks from a cutoff wheel or grinder will embed themselves in glass and plastic. Make note by keeping the sections of the old floorpan that have the parking brake cable lead, and speedometer cable clips so you can spot weld these items in place in the right spots before installing the floorpan. Also weld in your inboard seatbelt anchors prior to pan installation. It's harder to weld this stuff in upside down. Also measure your rear seat mounting hook location since you will have to install these as well.
With the old pan out. This is the perfect time to clean out inside the torsion bar crossmember and weld in reinforcements inside it to reinforce the torsion bar lugs to the crossmember, then treat it with Por-15 or some other rust inhibitor. Also the AMD floorpan outboard side stamped holes for the seatbelt anchors are not in the same spot as a 67-69 barracuda, they are further back. You will have to measure and drill these holes in the correct spot to line up with where your anchors are in your rocker panels. The inboard holes on the trans tunnel however are in the correct spot.
In my last pix showing the trunk pan, I fitted it into the car, then used a silver sharpie marker to draw the outline of the framerails and flanges that overlap, then pulled the pan back out and drilled for my spot welds in nice equal spacing using a unibit to make 1/4" holes. Floorpans are held in with big honking assed spotwelds. Then deburr the holes so the pieces fit tightly and use a weld thru primer on both mating surfaces.
Depending on what I have to clamp together, I use a mixture of cleco pins, visegrip clamps, toggle clamps and self tapping screws to hold the pieces together so I can rosette weld the holes. In the last pic you can see the trunk pan with the drilled holes, and the screws pinning it down in spots holding it tight to the rails prior to rosette welding. After you weld everything up, remove the screws your using to pin it in place, and fill those holes up with weld too.
I hope this all helps you out.
Matt
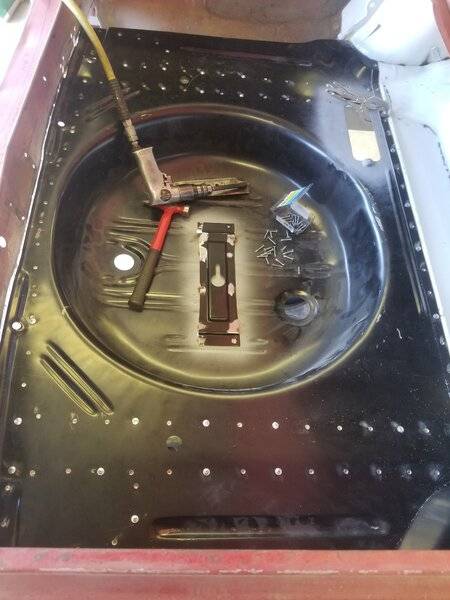