Alternator gauge is smoking
I always solder the stud heads to the brass lugs (green ovals on your picture) prior to installing any ammeter new or used. Use a hot 100 watt iron on the flat stud head, add a dab of solder to the intersection of the iron and stud head to initiate heat transfer, when that dab melts to where it wets the head of the stud add more solder to the rim of the stud head and it will flow around and under the head of the stud permanently bonding it to the brass lug of the ammeter. Ammeters with loose studs or deformed lugs can be saved in the same manner but all surfaces must be abraded to a shiny metal finish and the lugs must be straightened out prior to soldering. Doing this eliminates the perceived need to overtighten the ammeter attachment nuts. The wire eyelet nuts should be rather tight and the nuts need to be the ones with the radial lock grooves stamped into them. Prior to installation make sure the ammeter nuts and wire eyelets are shiny clean. Previously overheated ones will be dark gray or blued with oxidation and must be cleaned or replaced. If you replace a wire eyelet it must be crimped AND soldered to the wire, not just crimped. Crimped only will fail...every time. It is good practice to install a 12 gauge bypass wire directly from the alternator output stud to the starter relay stud. This will halve the current seen by the ammeter. Yes, I know the ammeter will not move as much as it did prior to the bypass, but it will still indicate charge/discharge, and it will not get hot anymore. You will have better headlights as a bonus.
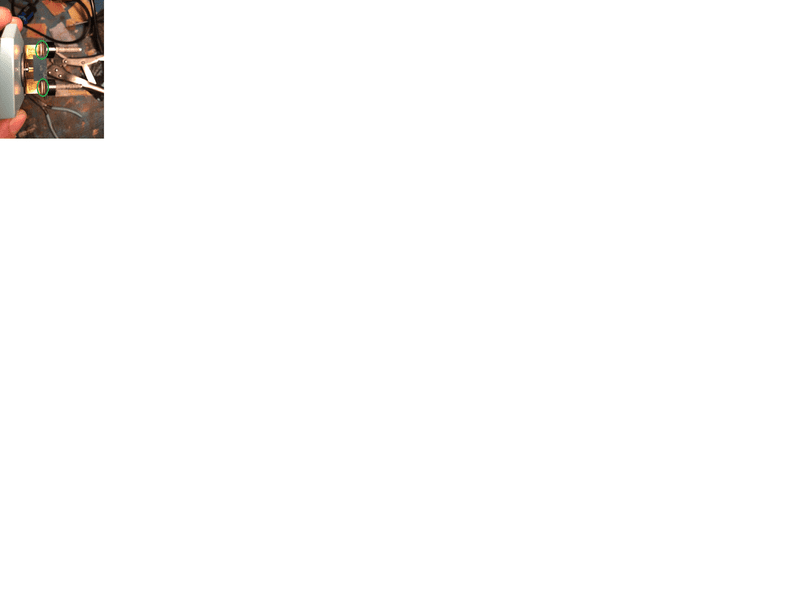