68 GT convertible project
Still waiting until the 120 day mark so I can wax the engine compartment and start assembling things in there. For now I've been working on applying the sound deadener to the floor. I was concerned about the garage temps being in the 30s/40s but it installed easily. I was planning on using Kilmat but ordered some stuff called Siless by accident. It's 80 mil, made from butyl and came in the same quantity as Kilmat so I used it. I covered the entire floor pan and up the firewall to where the factory insulation starts.
I installed some under the rear seat but just in the middle. That's where the resonance was. The area above the frame rails were solid so I didn't think I needed anything there. The section of the floor pan where the convertible top will sit sounded really hollow so I installed some there as well. I put a couple strips of sound deadener on the seat back brace that spans between the wheel wells. It sounded really hollow too. The metal wire covers along the rocker area were really beat up and rusted through in a few places. Replacements seemed really expensive for what they are so I made my own. I just bought the thinnest sheet metal the metal company carried(20 gauge) and drilled some holes along the length. Then I dimple died it for strength. I thought about different ways to attach it but ended up just using the sound deadener itself to hold the pieces in place. Finally, I put some aluminum tape on all the seams. The edges of the sound deadener are exposed and sticky. I put the tape on it so the carpet doesn't stick to the floor when the temp warms up.
I also got the 1/4 windows installed. What a PITA. I downloaded the 67 and 69 service manuals(the 68 manual isn't online) and read how they are supposed to be installed. The instructions left a lot to be desired. I ended up having to completely remove the rear stabilizer and unbolt the front track in order to move the glass forward inside the 1/4 so I could get the rollers attached. Before I could do any of that though, I had to sand/polish the stainless weather stripping channel at the leading edge of the glass. On my Challenger, the stainless was still attached to the glass so I carefully polished it as an assembly. On the Dart though, the glass setting tape had lost its hold and the stainless was loose. The convertible uses rivets to hold the stainless to the lift bracket at the bottom. Once I drilled off the rivet heads I was able to tap them out and remove the stainless piece. Here are the rivets holding the stainless to the lift bracket.
I discovered that I could drill and tap the lift bracket holes for some 8-32 button head screws. This made reattaching it at the base easy. There was still the issue with the glass setting tape though. I was nervous since I've never dealt with that stuff before. While ordering some weather strip adhesive online I stumbled on a product called "windshield and glass sealant". Its designed to fix leaks between glass and rubber gaskets. The tube was only $6 so I thought I'd give it a try. The glass setting tape was still well attached to the stainless...it had just come loose from the glass. So, after cleaning the old tape and the glass, I ran a bead of the sealant on the leading edge of the glass. Then I pushed the stainless in place. After attaching the bottom with the allen head screws, I wrapped tape around the glass to hold everything stationary while the sealant dried. So far it seems to be working great. If it fails, I'll just have to install new glass setting tape. The windshield sealant is basically thin, flowable silicone. It's quite a bit thinner then regular clear silicone you find in a big tube. Here are the button head screws used to attach the stainless to the lift bracket.
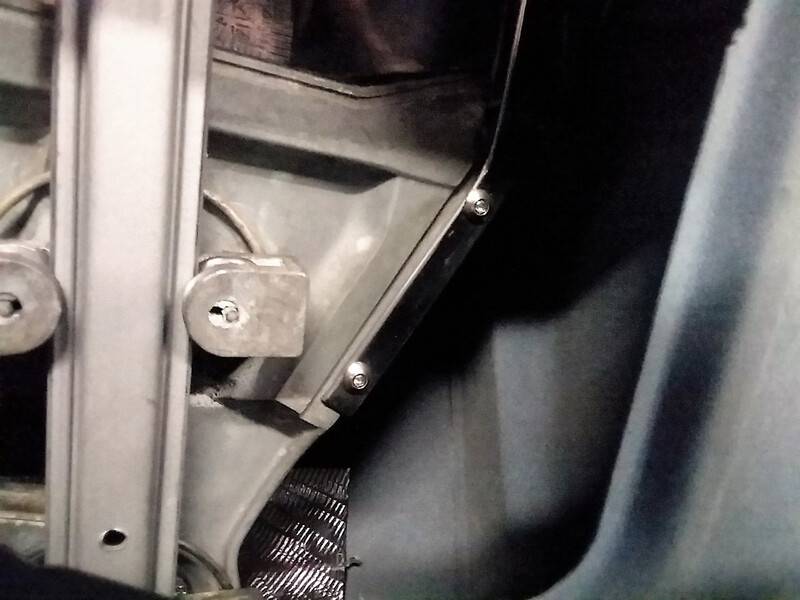