318 MAX fuel economy builds?
Long post, but ideas for better fuel economy-
1) Ignition system upgrades:
- The late '80s engines would already have a breakerless ignition.
- As for distributor cap, use only brass terminal versions. Both Blue Streak and NAPA's Belden brands offer brass terminal distributor caps. Use the rotor for the cap.
- Make sure the coil is robust. Older coils may not output sufficient energy for an effective spark.
- If you choose an aftermarket coil, be sure you either use a ceramic resistor, or choose a coil with dwell requirements compatible with the factory coil and ignition module. Too much dwell will burn out a high performance coil, while insufficient dwell will deliver a milk-toast spark.
- Pulstar Plugs pack a more powerful punch than standard plugs. They incorporate a mild "Peaking Cap" that delivers a significantly more intense spark (
Home - Pulstar Spark Plugs).
- Peaking Caps are relatively small capacitance capacitors (I've tested 150 pF upwards of 1000 pF) rated at a substantially high voltage (don't even think about using anything rated at less than 20 kV). 150-320 pF should be ample. They are placed in parallel to a NON-RESISTOR spark plug. Typical resistor plugs won't see any difference in the spark intensity. One lead of the cap goes to the ignition wire-to-plug connection (or COP-to-plug connection), and the other lead goes to ground.
- NGK, Champion, Autolite, Bosch, etc versions of "non-resistor" spark plugs still have about 1k ohms of resistance, while their normal resistor plugs have about 10k ohms. Brisk non-resistor plugs start at about 210 ohms (measured) for their "cheapies" down to less than 1 ohm for their Silver Aircraft No-Outer-Electrode plugs.
- Typical ignition wires have between 1k and 1.2k ohms per foot. An old hot-rod trick was to use solid core wires. Resistive wires were adopted due to AM radio interference from solid core wires. Modern computer controlled engines cannot run with solid core wires, as the EMF/RFI scrambles sensor signals rendering the ECU useless.... Granatelli discovered a way to use solid core wires in modern engines by incorporating an EMF/RFI suppression ferrite ring. The Granatelli wires are blue, but they also sell the same technology under the MPG Plus brand with a green jacket.
- Platinum makes for an excellent catalyst, but by nature lowers the voltage threshold requirement to initiate a spark jump to the point where substantially less fuel is ignited. The same can be said for other catalyst metals like iridium and probably ruthenium. Old fashioned copper core plugs with inconel electrodes deliver a higher spark intensity. The benefit of catalyst (platinum/iridium) electrodes is their ability to last 200k miles.
- Assuming your coil is capable, increasing spark gap will increase spark intensity. Some hot-rodders would jam a square of toilet paper into the distributor cap coil terminal to increase overall secondary ignition gap/resistance, which yielded a higher intensity spark.
- A much more thorough explanation can be found at
https://www.ecoceptor.com/MPGenie/ignition
2) Engine Considerations:
- First and foremost is the engine must be in good working condition. Cracked or worn rings that leak could never deliver the desired results. If a compression test delivers consistent healthy results, then move forward with confidence. If not, you may be spinning your wheels chasing an elusive and unobtainable goal.
- As the dynamic compression ratio is increased, the flame propagation rate is increased as well. This helps convert more of the chemical energy in the fuel to kinetic energy at the flywheel (in dyno terms, it's BSFC; in other words, better fuel economy); within the tolerance of the fuel (more shortly).
- The inverse of addition is subtraction. The inverse of multiplication is division. The inverse of the compression ratio is the
expansion ratio. Increased
static compression equals greater expansion ratio. George Arlington Moor pioneered a process of using a 16:1
static compression ratio with a custom camshaft profile that extended the intake lobe closing event to half way up on the compression stroke. The
dynamic compression ratio was a tolerable 8:1, but the expansion ratio was an advantageous 16:1 (look at how much more efficient diesel engines are with their 22:1 compression ratios versus gas engines with 9:1). Furthermore, this process would draw in an atomized air/fuel charge, swirl it around in a hot cylinder, vaporize some of the atomized fuel, then regurgitate some of it back into the intake plenum making it available for the next cylinder in the firing order as a more combustible mix. Mike Brown created a kit for popular Chrysler 360, Ford 302, and Chevy 350 engines back in the 1980's that included pistons and camshaft that utilized Moore's concept. The Toyota Prius uses the Atkins Cycle in their engines, similar to what Moore developed.
- The engine has many parasites; oil pump, water pump, windage, valve springs, friction, etc. If a stock oil pump keeps the engine alive, a high volume/pressure pump only creates additional parasites. If you only intend to rev the engine to 3800 RPM, high pressure valve springs only act as additional parasites. If the oil pump-to-block passages couldn't pass as identical twins, there will be flow restrictions increasing parasitic losses. You may want to port match oil/coolant passages. Casting flash that would cause flow restrictions in an intake or exhaust port could also cause restrictions in oil/coolant passages as well. This costs energy consumption.
- 30+ years ago I built a 360 using 318 cam, 318 open chamber heads (because the 302's weren't out yet), 318 intake & carb, and 318 exhaust manifolds. It was a 0.030" overbore using 1971 flat top pistons (no dish). As I recall, it ended up with a 10.8:1 static compression ratio. It was installed in a 1974 W-150 pick-up. It got 23-24 MPG HWY, and could pull a house on 87 octane fuel (quote from the truck owner).
3) Cylinder heads:
- Higher port velocities = higher efficiencies (BSFC). This has been extensively covered by the likes of David Vizard, Larry Widmer-TheOldOne, and numerous others. It isn't just port size, but eliminating dead zones where fuel can fall out of suspension.
- Abnormal protrusions can capture liquid fuel droplets and condense them into a small stream. Casting flash and machining marks can cost performance & economy. Simply smoothing a port can enhance both. Pay special attention to the valve guide areas, as well as the bowl transitions.
- Way back in the 1950's, OEMs found the benefits of "squish pads", where the piston almost smacks into a flat surface in the cylinder head. Look at early BB and 273 heads. For NOx emissions reasons, they abandoned the squish pad for open chamber heads from the mid 1960's till the late 1980's. The topic of 318 "302" heads (swirl port) involves not only higher compression -- tolerant to low octane fuel, but also reduced emissions (with the added benefit of better fuel economy and usable power). They have the venerable "squish pad".
- In the combustion chamber, sharp edges are your enemy. Look up "The Coanda Effect". Rounding sharp edges in the combustion chamber will allow the flame front to flow from one zone to another with less effort, promoting better flame propagation.
- Spend some time on "
www.TheOldOne.com" to see how Larry Widmer built a minuscule 1.8 liter Honda engine, 13:1 static compression, 30# turbo boost,
on 93 octane pump gas, and made over 500 HP, and got over 80 MPG!!!
- Intake port textures are critical. It has been known for several decades. Rough textures promote an exaggerated boundary layer. This forces the flow of air/fuel towards the center of the port, keeps the charge excited, and velocities high. Much discussion has been exchanged on using 40 or even 30 grit sanding rolls on intake ports to create a rough texture. There are also threads discussing using bent-bit chatter to create scallops in the surface. I personally developed what I called Powre Lynz that put "screw threads" into the intake port. The benefits are a variable boundary layer that responds positively to engine demands, better fuel suspension in the charge, and it will better vaporize fuel droplets that fall out of suspension and reintroduce them into the intake charge stream. Many CNC head porters now (thanks to me introducing David Vizard to my Powre Lynz) use a small ball bit and course resolution to create "ocean waves" in the intake ports.
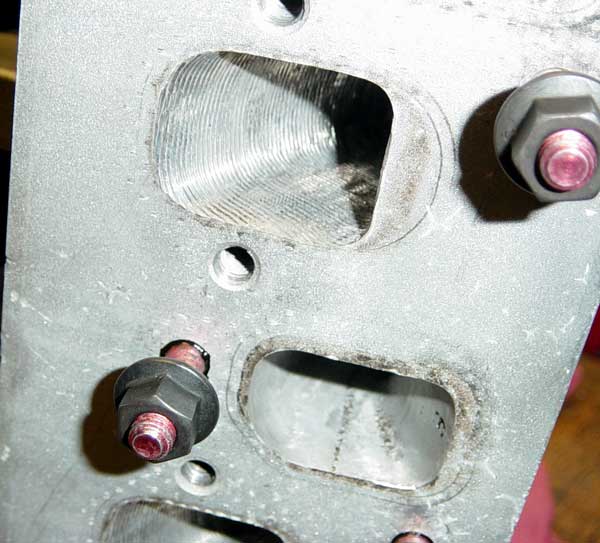
- You NEVER want a larger port from one component to lead into a smaller port in another component. The entire flow path includes the carburetor to intake manifold, to cylinder head intake port, to exhaust port, to exhaust manifold, to exhaust pipe path. Using a spread bore carb on a square bore intake creates unwanted obstruction. Using a 360/340 intake manifold with 318/273 heads creates unwanted obstruction. In the cylinder head, make sure the exhaust port in the combustion chamber is unshrouded (matched to the cylinder bore). Ideally, the intake manifold ports should be exactly the same dimensions as the ports in the cylinder head (as the "port" is continuous from manifold to head). The same for exhaust ports. The compromise when porting is to make the leading part port 1-2 mm smaller then the receiving part. In other words, the intake manifold port is 1-2 mm smaller than the port in the cylinder head. This prevents manifold alignment issues from creating unwanted port mismatch turbulence.
4) Induction-
- The concept is wet versus dry flow. Carburetors and TBI systems flow the entire intake tract wet -- air and fuel. Port fuel induction systems flow mostly dry, but still a portion of the tract wet. GDI flows only air, where the fuel is injected directly into the combustion chamber. Since the discussion is about a late '80s carbureted 318, the topic of focus is on wet flow throughout the entire intake tract.
- Many inventions/patents have focused on putting a screen or other "diffuser" under the carb to break larger fuel droplets into smaller droplets. I experimented with stainless screens with varying spacing, and different approach angles. My test bed was a '70 Duster with a 225 I custom built. It had a Super-6 2-bbl intake manifold. Using carb screens, I was able to squeak out 29.4 MPG best (well over my 18 MPG baseline). Later I found the Power Plate which was a 1" aluminum spacer that mounted between the carb and intake. It featured tapered cones under the carb bores with a 20 pitch screw thread. The body was heated with engine coolant. To install it, I had to remove my carb screen. Needless to say, I went from a best of 29~ MPG to 44.7 MPG!! Normal driving was still in the mid- to high-30 MPG range.
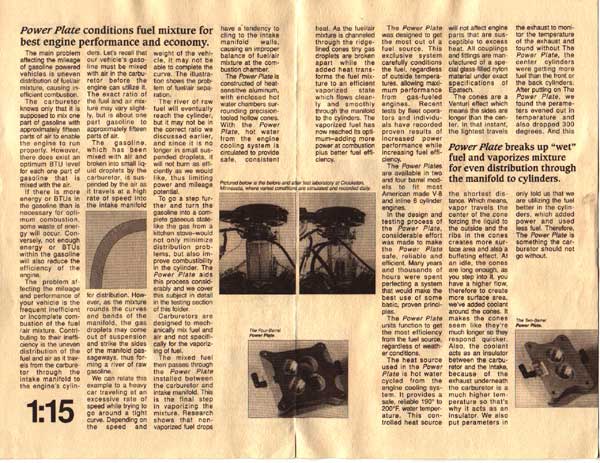
[Wow, long post. Should quit for now.]