Classic Auto Air Belt alignment fix
Last year when doing the restomod on my 1970 Dart GT, I purchased and installed a Classic Auto Air AC/heater kit. It wasn’t cheap and was billed as a Perfect Fit kit – it was anything but. The one that I got was for a 1967-76 A body and specifically used a factory AC crank pulley (3 groove), water pump pulley and 2 groove pulley alternator. There were a number of things that needed to be changed or adapted in this kit but I won’t go into all that here. What this is about was the most vexing and difficult to remedy issue with the kit. When all was installed as designed the double groove alternator pulley, the double groove AC compressor pulley, and the two grooves for that purpose on the crank pulley do not line up – or rather only one groove lines up. The bracket that comes with the kit to mount the compressor that is also part of the kit is a tight fit. The back of the compressor is right up against the thermostat housing on the intake, as a matter of fact the directions even talk about grinding a bit on the housing to provide sufficient clearance for the compressor. This means that the compressor cannot possibly move any further back. This results in the compressor groove that is closest to the engine aligning with the grooves on the crank pulley that are the farthest from the engine.
This means that the AC compressor and alternator run on just one belt. I called Classic Air and they sent me to Bouchillon because they make the kit to mount the compressor (indeed their name is engraved on the main bracket). Bouchillon told me you only need one belt and it would all be fine. Once the belts got a little broken in I found that this was not the case. No matter how tight I adjusted the single belt, just as soon as it got hot outside (just when you need the AC) or the belt got warmed up, the belt squealed like a pig whenever the compressor engaged. This includes when the compressor engages to dehumidify the defrost air.
Here is the fix that I used to get the pulleys aligned. My situation was complicated because the current arrangement includes a power steering pump and water pump pulley that run on a single belt in front of the AC/alternator belts. Since the compressor is fixed, the alternator and crank pulleys need to move away from the engine the distance of one belt groove so that 2 grooves are aligned. You can space the alternator forward by moving the forward alternator mounting ear to the front of the forward compressor bracket, then using spacers to make the whole assembly tight. One groove width including the metal around the actual groove Is ½ inch.
The crank pulley could be spaced forward with a custom made spacer behind the crank pulley and longer bolts, but I opted to dig through a bin of factory crank pulleys and find one that moved the grooves to the right place. I couldn’t find exactly what I needed – you need two matched depth grooves toward the engine for the AC/alternator double belts and a single groove in front of that for Power steering/water pump belt. What I found was a readily available 4 groove crank pulley that worked perfectly. You have to be sure that the crank pulley diameters are very close to the original AC crank pulley. I went to a machine shop and they lopped off the extra 4th groove from the front, mostly for aesthetic reasons. This is not necessary.
The result of this work was a two belt set up for compressor and alternator, but the belt furthest from the engine was now in the same place as the water pump and power steering pulleys so they also had to move forward one pulley groove. You could put a spacer behind the water pump pulley, but that would move both the groove and the location of the fan (to a less than optimal location). Back to the old pulley bin, and I was able to find a factory pulley that was the same diameter, but was 1 groove shallower, leaving the fan location unchanged, but moved the groove forward to the correct location. Moving the PS forward was pretty easy by spacing all the bolts attaching it to the block one groove farther from the block and using ½ inch longer bolts. Don’t try to do this by spacing within the multiple brackets holding the pump.
Here are some pics of the resulting set up.
I hope this makes your life with this system easier! Much of the Classic Air system including the design of the electrical parts, the new AC/heater box under the dash, most of the controls, the quality of the compressor are excellent. They just needed to install a few of these and fix all the little **** that each of us now has to resolve on our own. I have little good to say about Bouchillon, who clearly knew that the one belt system both looked like crap and was vastly inferior to the factory 2 belt drive, and yet couldn’t be bothered to fix the alignment.
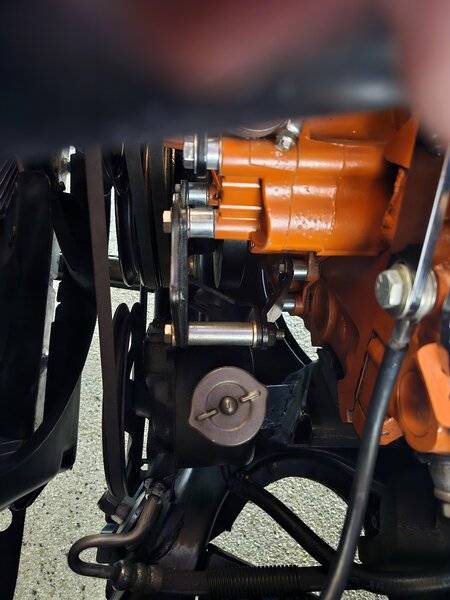