mattmatthew
^_^
Short update.
Finished fabbing up the front hard lines, and the front part of the rear line up to the proportioning valve.
Put the KYB's in...
Let down the car off the jack stands. First time it's been off the jack stands in over 6 months. In hindsight I should've cranked the torsion bar bolts all the way up, because now she sits lower than I can get the jack back under, lol. Woops. I'll figure something out. But for now this is a great motivator to finish up the final parts of this brake rebuild.
Finished fabbing up the front hard lines, and the front part of the rear line up to the proportioning valve.
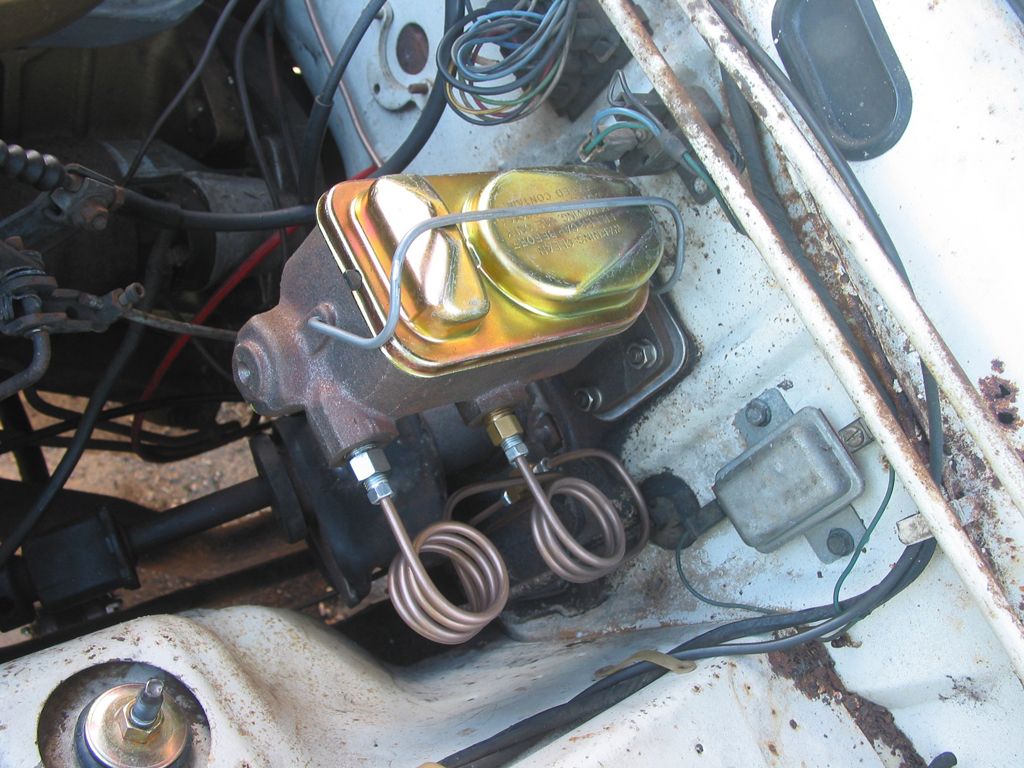
Put the KYB's in...

Let down the car off the jack stands. First time it's been off the jack stands in over 6 months. In hindsight I should've cranked the torsion bar bolts all the way up, because now she sits lower than I can get the jack back under, lol. Woops. I'll figure something out. But for now this is a great motivator to finish up the final parts of this brake rebuild.
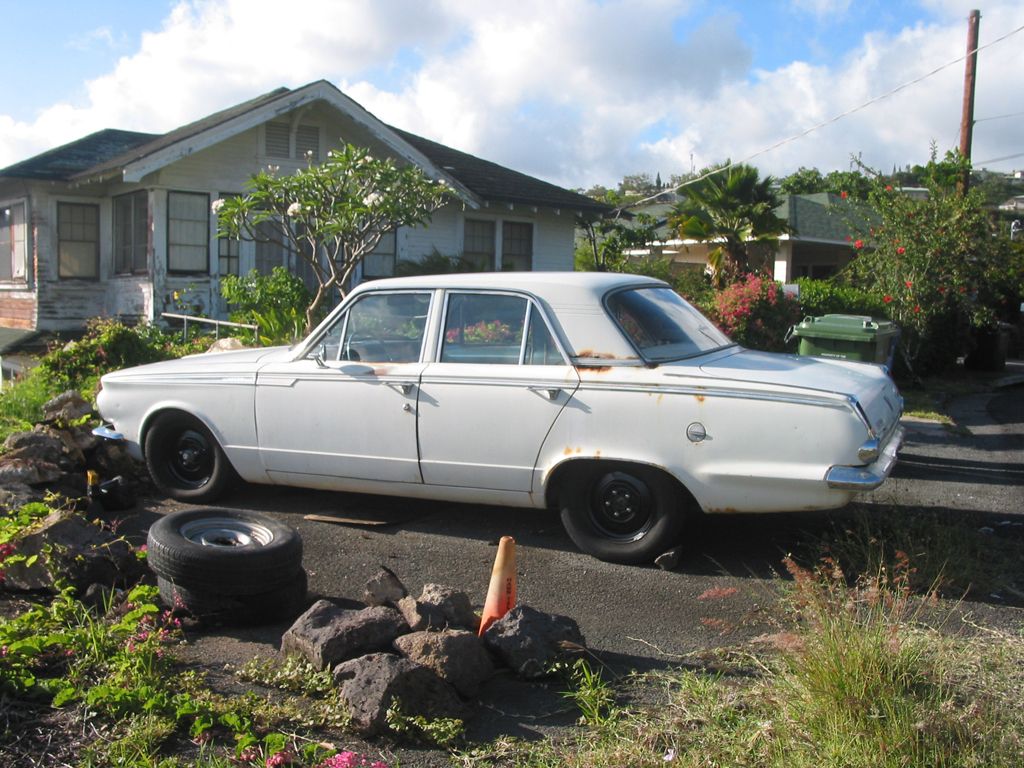