alain
Turbo's, Turbo's, Turbo's
I joined FABO a few days ago and am liking the community. In my newbie thread http://www.forabodiesonly.com/mopar/showthread.php?t=89883 I already posted some pics of my Dart (which is currently a project), but I think it may be better to continue the updates here.
I bought my Dart back in 1998 from a good friend who had it imported into Holland from Monrovia, California in 1997. It's a basic Dart with no options and originally had a 273ci. Some previous owner in The States had swapped in the 318. When it arrived in Holland it had an exploded bench seat, a bad motor and a not so fresh 904 transmission. My mate then bought a '74 Dart locally as a parts car and also ran into an '86 Le Baron. He swapped the motor in from the '74 Dart and mixed a combination of '74 Dart and '86 Le Baron parts to convert the drum brakes to power discs. The large bolt pattern discs on the front meant the rear had to be redrilled as well, so the axles of the 7 1/4" were fitted with studs in a large pattern. 14" Wolfrace rims were added and he was good to go.
After just over a year, I bought the Dart off him and the first task was to rebuild a trans as the 904 was starting to slip more and more in 3rd gear. It was the very first trans I'd rebuilt and I was really happy that it all worked out first go. I completed it ith a Gil Younger shift kit and increased the line pressure a bit.
The thermoquad had a gigantic flat spot in it and being no expert with these crabs, I couldn't get it out. I bought a 650 dumper pumper Holley and after rejetting it, the car was running great.
I went to plenty of weekend meets with it and even went over to England (Santa Pod Raceway) for the Mopar Nationals with it on one occasion.
Then came 2001. I started developing an interest for turbocharging (after having owned a Renault 5 GT Turbo). I read and read and talked to guys in Australia that were already doing this and then set out to build my own motor. Building motors wasn't a new experience to me cause I'd been building motors (mainly for others) for years. But a turbo motor was a first for me. The initial plan was to build a low budget try it out kind of project, but as I went along I got more and more enthoused and one thing lead to another and before long, I was building more of a race car than just a modified street car. I have always kept the intention of streetability in mind and even welded new pads on the rearend to be able to put the leaf springs back on if necessary.
I started physically building the motor over Christmas in 2002 and in February 2003 I drove the Dart into the garage for the very last time before taking it apart. First on the agenda was to create more room for the tires, so I cut out the wheel wells and moved them inboard (flush with the chassis). After that I cut holes in the floor and started welding in a 4-link. I only had a spare 10 bolt Chevy rear with 3.73 gears and a posi lying around at the time and decided to use it. It was shortened and fitted with C-clip eliminators and the brackets for the 4-link bars. To make room for the coil overs, I also removed the spare tire well as the rearend is moved slightly back to accomodate 28" slicks without making any changes to the wheel arches.
Next up were the headers. I bought a load of 90 bends and some straight pipe and started configuring the pipes. I wanted to route each pipe to the collector so that the cilinders firing as close as possible to 180 degrees apart were blowing into the same turbine half (split housing). I also wanted to be able to access the plugs in a decent manner and be able to fit the headers in without having to take half the car apart to do so. All of the above criteria was met and I'm very pleased with the end result.
I originally wanted to go blow through but after thinking long and hard about this, I was convinced EFI is the only right way to go about it. EFI is better for driveability and has a much wider operating band than a carb. Carbs work well in a certain rpm range. That can be from idle to 3500 rpm, from 2500 to 5000 rpm, etc, but never from idle to max rpm. That's the beauty of EFI. It works over the entire rpm band. It allows you to do tiny adjustments to whichever part of the range without directly effecting other area's. I decided upon an Autronic SM2 (SM4 wasn't available at the time and this was the latest version) with a 1.93 chip set.
Just last October I finally got so far as to put the new motor in the bay. I immediately started building a 727 for it and outfitted it with Alto Red's, Kolene steels, heavy duty bands, 5 pinion sungear, an aftermarket bolt in Roller Clutch and a Transgo TF2 kit. During my last visit to The World Street Nats in Orlando in 2009 I bought a cast aluminum trans pan and then went to mount the transmission.
Mounting the transmission wasn't all that easy either. When mating it to the bell housing flange, it wouldn't go all the way together. I found that the converter pilot wasn't going into the hole in the crank. Measuring the difference I found I have a small pilot hole crank from a pre 68 273. I knew I had a 273 forged crank of course, but at the time wasn't aware that there were different sized pilot holes. I had 2 options and that was to take the motor out again and tear it apart to put another crank with a large pilot hole (which I incidently have as a spare) or try to enlarge the hole in the current crank. I decided to try the last option as it would save a lot of work. I made a center guide that fit perfectly in the hole of the crank. I made a cutting tool to make a hole exactly the same diameter as an original large pilot hole and preceded to enlarge the hole in the crank working underneath the car. Luckily I have a 4 post car hoist in my garage, so I have plenty of working space. It took me about 3 hours to get the hole as I wanted it and voila, the converter nose fit in the hole. Another problem tackled.
Now I'm in the process of mounting new 1/2" fuel lines to the fuel cell mounted in the trunk. I'm going to be running E85. I have also completed the cold side piping (except for the clamps) and getting there little by little. The hood doesn't fit anymore, so recently I picked up a lift off fiberglass hood at a friends place. I need to modify the hole slightly and then bond on a scoop. I think I'll go for a cowl induction scoop.
Summary of the specs on my Dart:
318ci, twin Garrett GT32's, Transgo equipped 727 with Alto red's and Kolene steels, 4 link rear, mini-tubbed, beefed up 10-bolt with 3.73 and posi (yeah I know, it's a Chevy rear - but ran into it), Autronic SM2 (1.93 chip set) ECU for the multipoint injection, Edelbrock Super Victor EFI intake, Edelbrock RPM heads (ported by Hensley Racing), Custom 8.0:1 Ross Forged Racing pistons, custom grind Comp Cams roller cam, Crane Gold Race Roller Rockers, 273 forged crank, Eagle ESP-3D H-beam rods and ARP studs throughout.
If you have any questions, let me know. I'll try to keep this thread updated as best I can.
I bought my Dart back in 1998 from a good friend who had it imported into Holland from Monrovia, California in 1997. It's a basic Dart with no options and originally had a 273ci. Some previous owner in The States had swapped in the 318. When it arrived in Holland it had an exploded bench seat, a bad motor and a not so fresh 904 transmission. My mate then bought a '74 Dart locally as a parts car and also ran into an '86 Le Baron. He swapped the motor in from the '74 Dart and mixed a combination of '74 Dart and '86 Le Baron parts to convert the drum brakes to power discs. The large bolt pattern discs on the front meant the rear had to be redrilled as well, so the axles of the 7 1/4" were fitted with studs in a large pattern. 14" Wolfrace rims were added and he was good to go.
After just over a year, I bought the Dart off him and the first task was to rebuild a trans as the 904 was starting to slip more and more in 3rd gear. It was the very first trans I'd rebuilt and I was really happy that it all worked out first go. I completed it ith a Gil Younger shift kit and increased the line pressure a bit.
The thermoquad had a gigantic flat spot in it and being no expert with these crabs, I couldn't get it out. I bought a 650 dumper pumper Holley and after rejetting it, the car was running great.
I went to plenty of weekend meets with it and even went over to England (Santa Pod Raceway) for the Mopar Nationals with it on one occasion.
Then came 2001. I started developing an interest for turbocharging (after having owned a Renault 5 GT Turbo). I read and read and talked to guys in Australia that were already doing this and then set out to build my own motor. Building motors wasn't a new experience to me cause I'd been building motors (mainly for others) for years. But a turbo motor was a first for me. The initial plan was to build a low budget try it out kind of project, but as I went along I got more and more enthoused and one thing lead to another and before long, I was building more of a race car than just a modified street car. I have always kept the intention of streetability in mind and even welded new pads on the rearend to be able to put the leaf springs back on if necessary.
I started physically building the motor over Christmas in 2002 and in February 2003 I drove the Dart into the garage for the very last time before taking it apart. First on the agenda was to create more room for the tires, so I cut out the wheel wells and moved them inboard (flush with the chassis). After that I cut holes in the floor and started welding in a 4-link. I only had a spare 10 bolt Chevy rear with 3.73 gears and a posi lying around at the time and decided to use it. It was shortened and fitted with C-clip eliminators and the brackets for the 4-link bars. To make room for the coil overs, I also removed the spare tire well as the rearend is moved slightly back to accomodate 28" slicks without making any changes to the wheel arches.
Next up were the headers. I bought a load of 90 bends and some straight pipe and started configuring the pipes. I wanted to route each pipe to the collector so that the cilinders firing as close as possible to 180 degrees apart were blowing into the same turbine half (split housing). I also wanted to be able to access the plugs in a decent manner and be able to fit the headers in without having to take half the car apart to do so. All of the above criteria was met and I'm very pleased with the end result.
I originally wanted to go blow through but after thinking long and hard about this, I was convinced EFI is the only right way to go about it. EFI is better for driveability and has a much wider operating band than a carb. Carbs work well in a certain rpm range. That can be from idle to 3500 rpm, from 2500 to 5000 rpm, etc, but never from idle to max rpm. That's the beauty of EFI. It works over the entire rpm band. It allows you to do tiny adjustments to whichever part of the range without directly effecting other area's. I decided upon an Autronic SM2 (SM4 wasn't available at the time and this was the latest version) with a 1.93 chip set.
Just last October I finally got so far as to put the new motor in the bay. I immediately started building a 727 for it and outfitted it with Alto Red's, Kolene steels, heavy duty bands, 5 pinion sungear, an aftermarket bolt in Roller Clutch and a Transgo TF2 kit. During my last visit to The World Street Nats in Orlando in 2009 I bought a cast aluminum trans pan and then went to mount the transmission.
Mounting the transmission wasn't all that easy either. When mating it to the bell housing flange, it wouldn't go all the way together. I found that the converter pilot wasn't going into the hole in the crank. Measuring the difference I found I have a small pilot hole crank from a pre 68 273. I knew I had a 273 forged crank of course, but at the time wasn't aware that there were different sized pilot holes. I had 2 options and that was to take the motor out again and tear it apart to put another crank with a large pilot hole (which I incidently have as a spare) or try to enlarge the hole in the current crank. I decided to try the last option as it would save a lot of work. I made a center guide that fit perfectly in the hole of the crank. I made a cutting tool to make a hole exactly the same diameter as an original large pilot hole and preceded to enlarge the hole in the crank working underneath the car. Luckily I have a 4 post car hoist in my garage, so I have plenty of working space. It took me about 3 hours to get the hole as I wanted it and voila, the converter nose fit in the hole. Another problem tackled.
Now I'm in the process of mounting new 1/2" fuel lines to the fuel cell mounted in the trunk. I'm going to be running E85. I have also completed the cold side piping (except for the clamps) and getting there little by little. The hood doesn't fit anymore, so recently I picked up a lift off fiberglass hood at a friends place. I need to modify the hole slightly and then bond on a scoop. I think I'll go for a cowl induction scoop.
Summary of the specs on my Dart:
318ci, twin Garrett GT32's, Transgo equipped 727 with Alto red's and Kolene steels, 4 link rear, mini-tubbed, beefed up 10-bolt with 3.73 and posi (yeah I know, it's a Chevy rear - but ran into it), Autronic SM2 (1.93 chip set) ECU for the multipoint injection, Edelbrock Super Victor EFI intake, Edelbrock RPM heads (ported by Hensley Racing), Custom 8.0:1 Ross Forged Racing pistons, custom grind Comp Cams roller cam, Crane Gold Race Roller Rockers, 273 forged crank, Eagle ESP-3D H-beam rods and ARP studs throughout.
If you have any questions, let me know. I'll try to keep this thread updated as best I can.
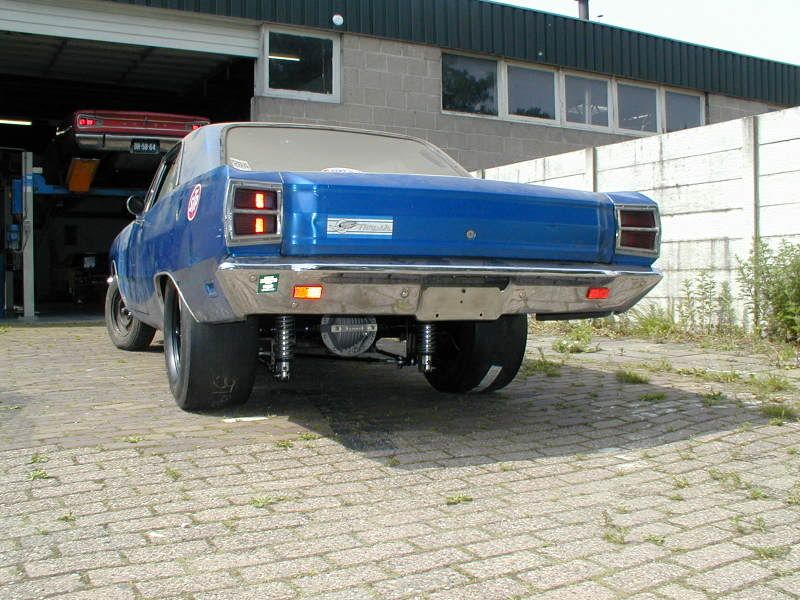
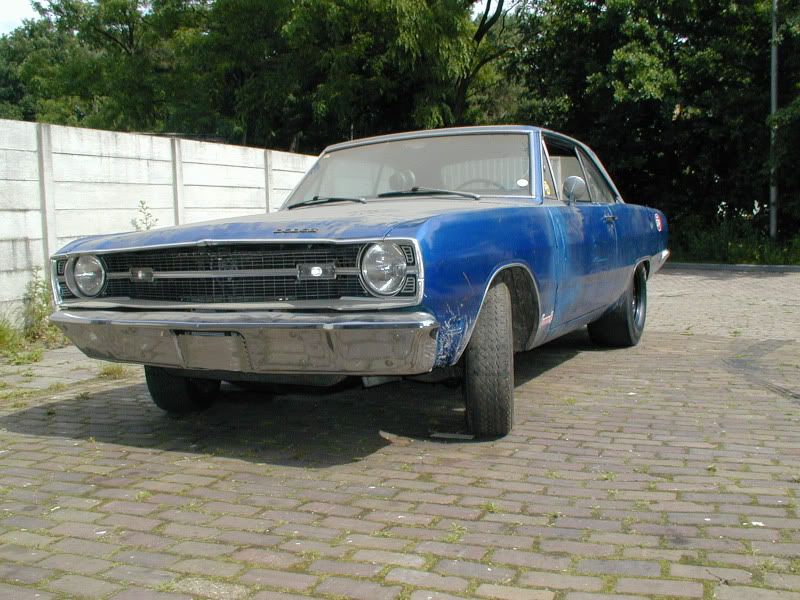
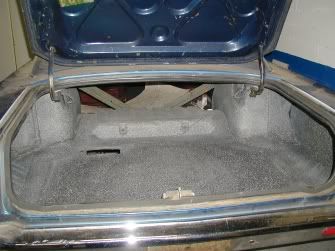
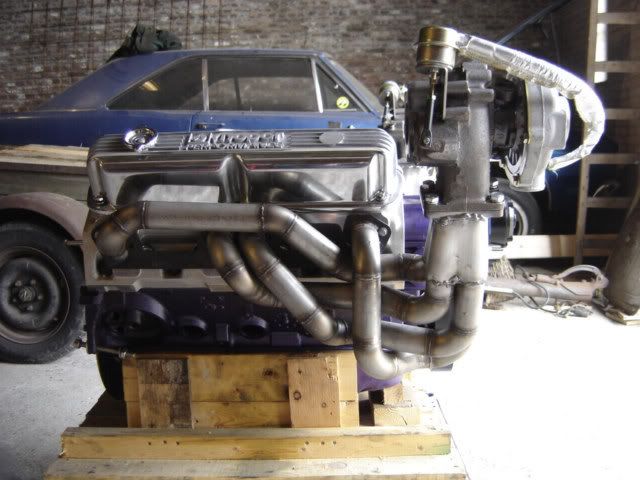
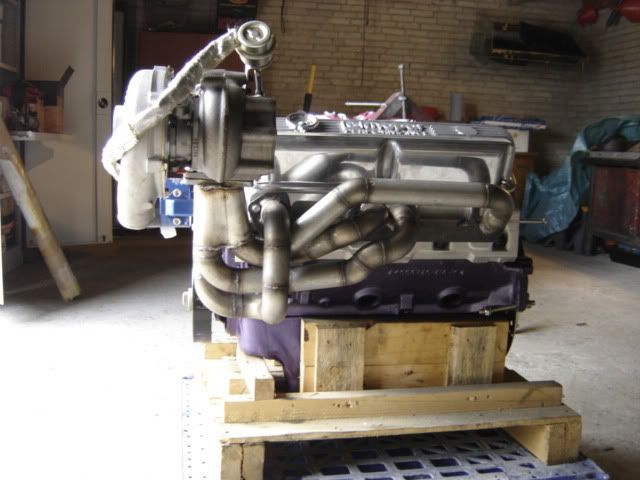
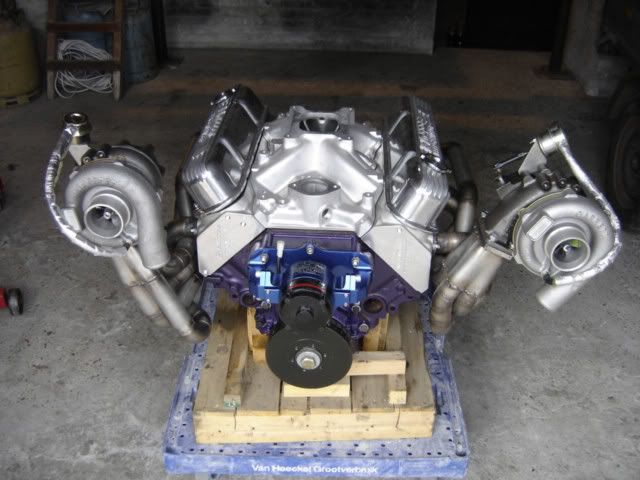
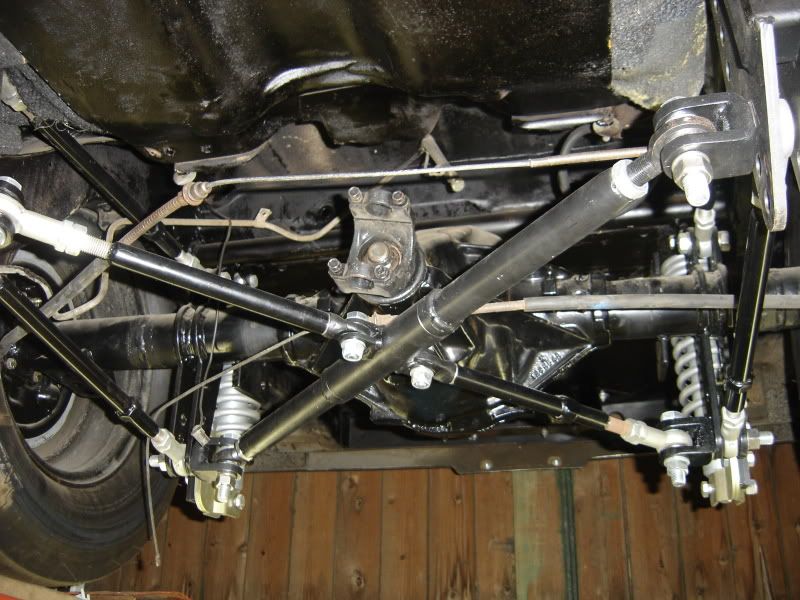
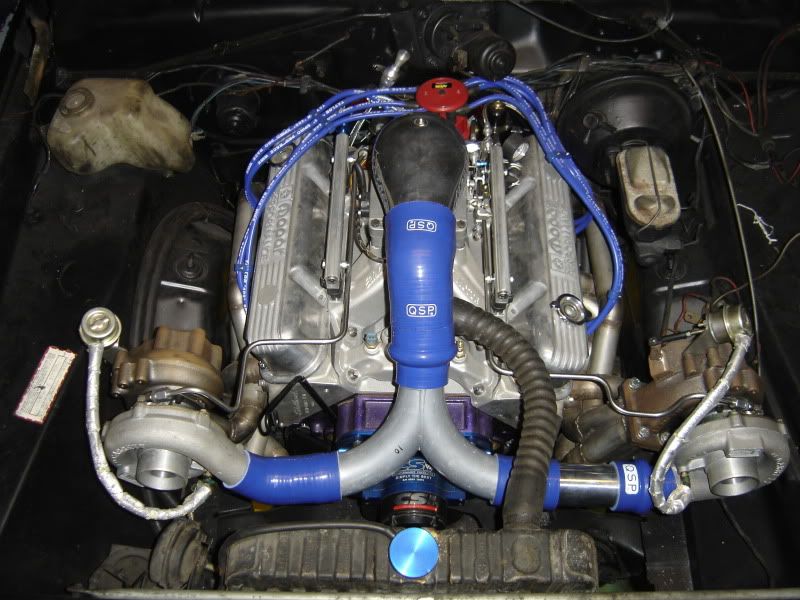