I bought a SS coolant overflow tank for the radiator. It came with two 1/4" tubes sticking out the bottom. One is an overflow purge and the other is the inlet to the tank. The overflow nipple on the radiator is larger than 1/4" so I needed to figure out a way to connect the two. I ended up cutting off the 1/4" inlet tube and drilled out the bottom of the tank. Then I installed a 6AN fuel cell fitting. I had some aluminum fuel line sitting around so I bent up a piece to connect the tank to the radiator. I'll just have a short length of hose from the line to the rad nipple.
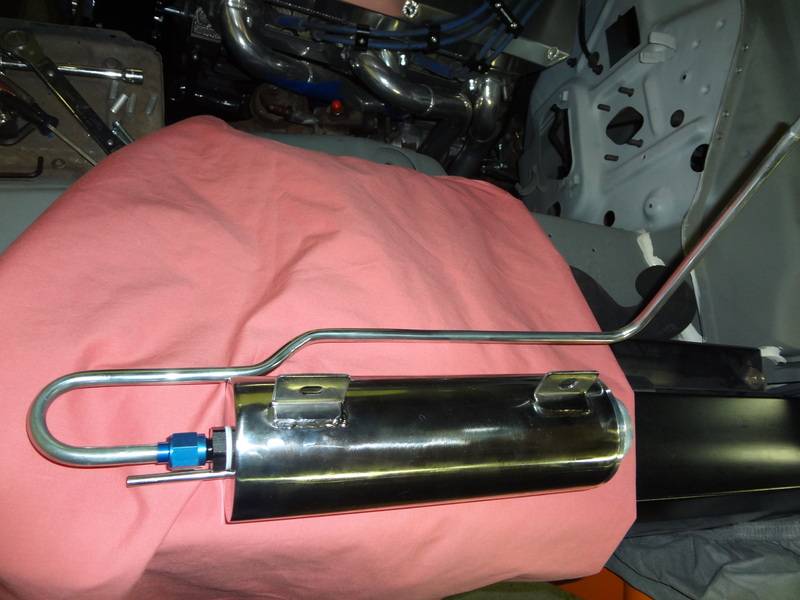
Here is what the shroud and overflow tank look like when installed. The shroud hasn't been polished yet in this picture. You can see that the shroud fits over the radiator's side brackets. It will be held on with (4) polished stainless button head bolts. I replaced the metric rivnuts that came on the radiator with 1/4-20 ones. There are spacers on the inside so the shroud doesn't get compressed when the fasteners are tightened down. The overflow tank uses one of the shroud attaching points. For the second attachment point, I installed a rivnut into the shroud itself.
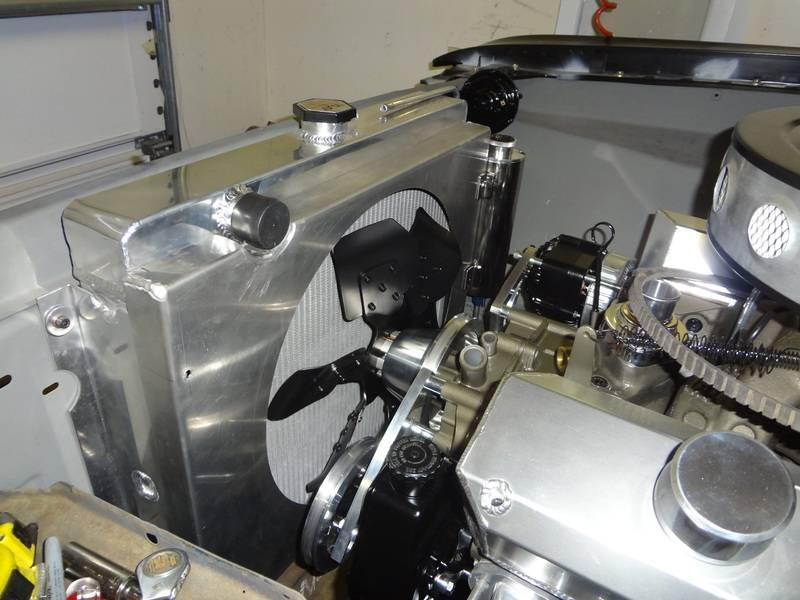
I started playing around with plug wire routing. I have some old Taylor wires that I used for mockup. I bought some cheap aluminum plug wire separators on E-bay. I really like the way they look. Most wires sets have the wires way too long and the finished product looks messy. I should be able to cut a set of wires to the exact length I need. These wire separators will make it really easy to get the look I want. I will be removing the logos before assembling them for the final time.
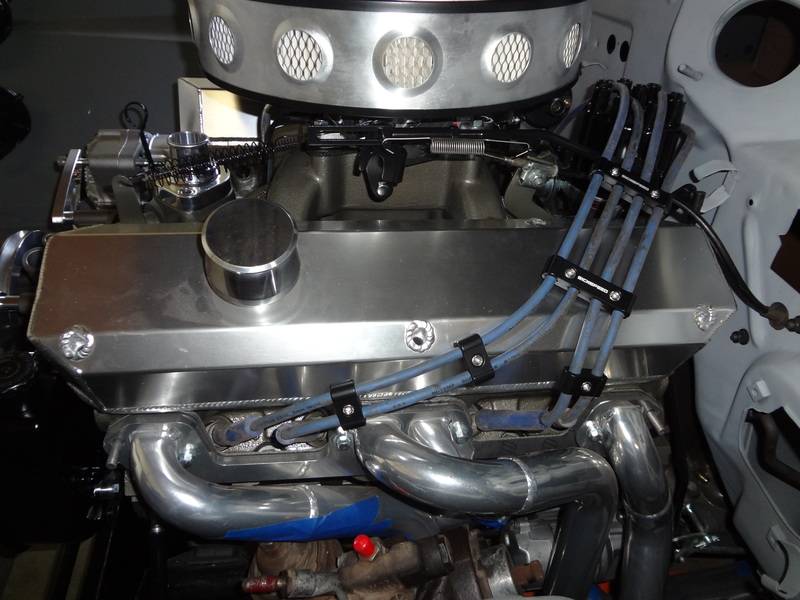
Here is what the shroud and overflow tank look like when installed. The shroud hasn't been polished yet in this picture. You can see that the shroud fits over the radiator's side brackets. It will be held on with (4) polished stainless button head bolts. I replaced the metric rivnuts that came on the radiator with 1/4-20 ones. There are spacers on the inside so the shroud doesn't get compressed when the fasteners are tightened down. The overflow tank uses one of the shroud attaching points. For the second attachment point, I installed a rivnut into the shroud itself.
I started playing around with plug wire routing. I have some old Taylor wires that I used for mockup. I bought some cheap aluminum plug wire separators on E-bay. I really like the way they look. Most wires sets have the wires way too long and the finished product looks messy. I should be able to cut a set of wires to the exact length I need. These wire separators will make it really easy to get the look I want. I will be removing the logos before assembling them for the final time.