killnine
Well-Known Member
So I bought a 8.75 rear end pretty much complete minus brake hardware, and just started digging into it to replace what should have been the only thing that it needed, the seals. It's got tapered bearings on the axles. I got the axles out, and after looking into the housing I notice that the housing end seems to be welded on about half an inch off center. It seems to be on 'straight'; I haven't checked whether the flange face is 90 degrees to the rest of the housing, but it's definitely not on centered.
The other end isn't perfect either, but is only a little noticeable. So now I am starting to think this housing was cobbled together, or had the housing end repaired at one time (badly). I'm pretty sure this wouldn't have happened from the factory. The measurements all add up, so
I'm not doubting its origin, just what happened, and how to recover from this now. The person I bought it from is a member and seems trustworthy. This is more about what the hell do I do now. Anything? Run it? Grind it cut it and weld it? I don't have the time or money to ship it back or look for a new housing.
I was really hoping to get something I didn't have to fabricate (or when I do it, some other word that isn't quite as honorable). I need to replace my 7.25 which seems to be ready to kill me with this by the week of Christmas so I can go see my wife 13 hours away.
Here are some pictures.
Other, not so bad side last
The other end isn't perfect either, but is only a little noticeable. So now I am starting to think this housing was cobbled together, or had the housing end repaired at one time (badly). I'm pretty sure this wouldn't have happened from the factory. The measurements all add up, so
I'm not doubting its origin, just what happened, and how to recover from this now. The person I bought it from is a member and seems trustworthy. This is more about what the hell do I do now. Anything? Run it? Grind it cut it and weld it? I don't have the time or money to ship it back or look for a new housing.
I was really hoping to get something I didn't have to fabricate (or when I do it, some other word that isn't quite as honorable). I need to replace my 7.25 which seems to be ready to kill me with this by the week of Christmas so I can go see my wife 13 hours away.
Here are some pictures.
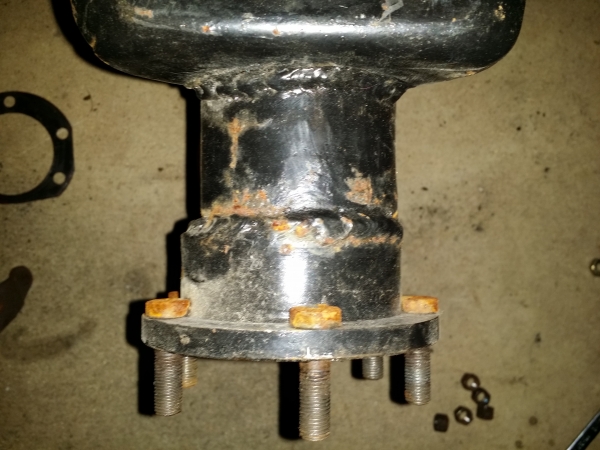
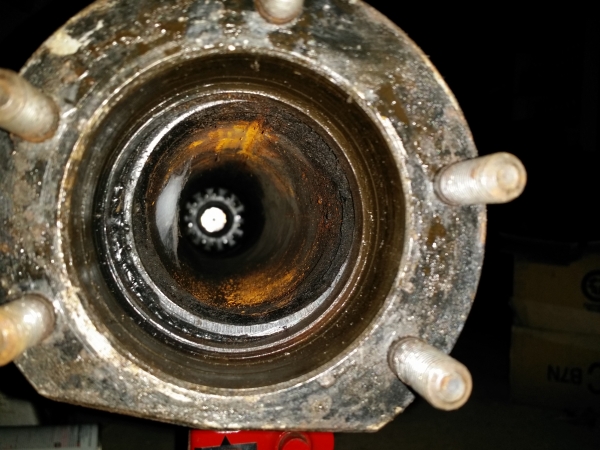
Other, not so bad side last
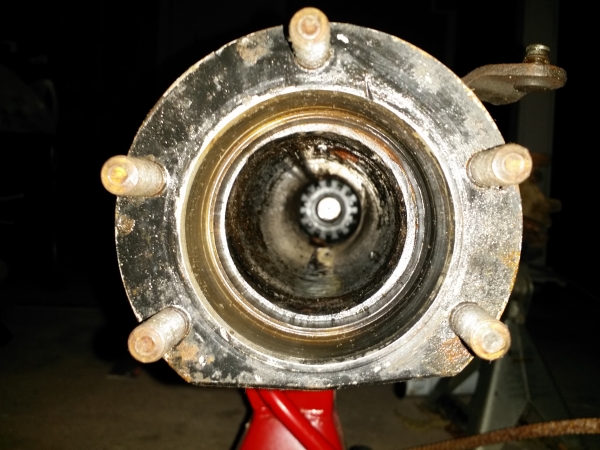